
tel Piet: +31 6 38 82 23 01
tel Vivienne: +31 6 81 48 78 79
info@vips-tc.com
Our projects
From quote to training and installation, you're secure in our care.
Over the years, we have successfully completed a wide range of projects, from small to very large, always with the same enthusiasm and dedication. But our commitment doesn't end with installation. I'm here to support you with updates, expansions, instructions, spare parts, automation projects or even just a friendly chat. In the close-knit world of specialized grinders, we'll certainly cross paths often. Let's keep pushing the boundaries together!
60 m line, 2 wide belt precision grinders, measuring and handling
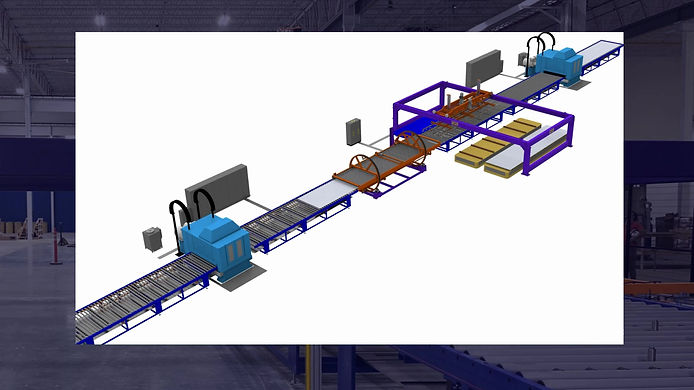
Here you see an example of a project we recently completed: a 60-meter fully automated machine line with Level 2 integration, featuring two 81 series precision grinders. What do we mean by automated? Not just picking and flipping, but also advanced automatic measurement with equipment that offers thickness measurement up to a measuring accuracy of +/- 5 microns and sampling times up to 1 ms.
Reciprocating table
​Here we show a video of a reciprocating vacuum table machine with a pick and place and turnover device.
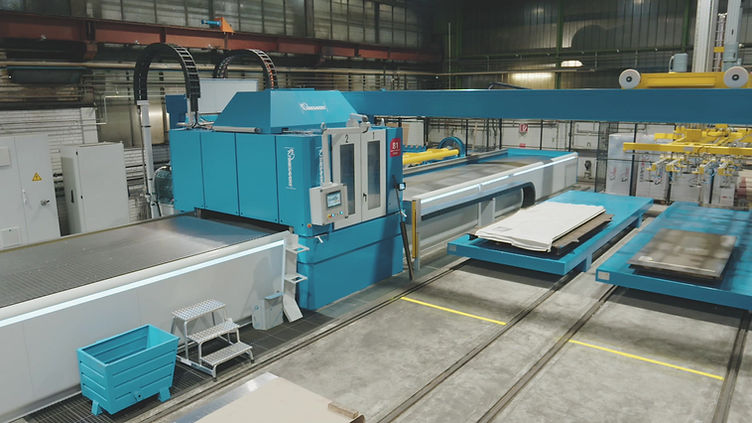
customer testimonial
Caleb, an aerospace industry customer, shares his experience of working with Piet Kooman:
Piet is unique in the grinding business because he combines strong technical knowledge of his equipment with extensive commercial experience. He took the time to understand our production needs and matched us with the right machines, ensuring a perfect fit both technically and financially.
During the installation, Piet wasn't just a sales representative—he was onsite, working hands-on seven days a week. His dedication didn't end there; he also provided comprehensive training for our operators, using materials he developed himself. The combination of theory, classwork, and hands-on practice made the training highly effective, and our team greatly valued his relatable and engaging approach.
Having Piet manage sales, installation, and training meant we had a single point of accountability throughout the process, minimizing confusion and ensuring all our expectations were met. Beyond his equipment expertise, Piet's extensive network in the industry helped us connect with other suppliers, providing valuable support beyond the immediate project.
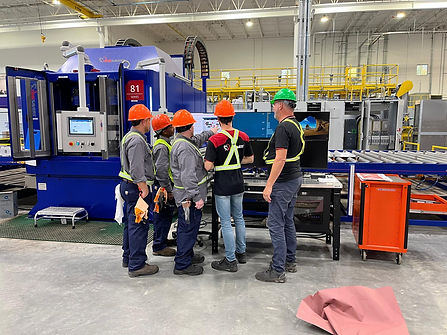
More insights in Level 2 automation project
Level 2 automation is an automation level within industrial processes that focuses on production control and monitoring. It sits above machine control systems (Level 1, such as PLCs or DCS systems) and below production planning and business systems (Levels 3 and ERP systems). The purpose of Level 2 automation is to enhance production efficiency by collecting and analyzing data in real-time, helping operators make more informed decisions and optimize the production process.
​
Key features of Level 2 automation:
​
-
Process Monitoring and Optimization: Level 2 systems provide real-time monitoring of the production process, controlling parameters such as temperature, pressure, speed, and other relevant data.
-
Data Analysis and Reporting: These systems collect detailed data from machines and use this data for analysis, helping to identify trends and deviations. This enables potential issues to be detected and corrected early on.
-
Quality Control and Traceability: Thanks to product traceability, every item in the production line can be tracked. This ensures that deviations can be quickly identified, leading to a higher quality of the final product.
-
Communication between Machines and Operators: Level 2 systems communicate with both the machine control layer (Level 1) and the business layer (Level 3), allowing operators to intervene directly when needed, without having to physically access the machines.
Application in the metalworking industry:
​
In the metalworking industry, Level 2 automation is often used to optimize the production process, particularly in processes such as grinding and finishing metal plates. By integrating Level 2 systems, companies can save time, improve production efficiency, and reduce costs. An example is the automatic tracking of the thickness and finishing quality of metal plates in real-time, enabling quick adjustments without manual inspection. This automation not only improves productivity but also ensures higher accuracy and traceability of products, leading to better quality control and reduced waste.
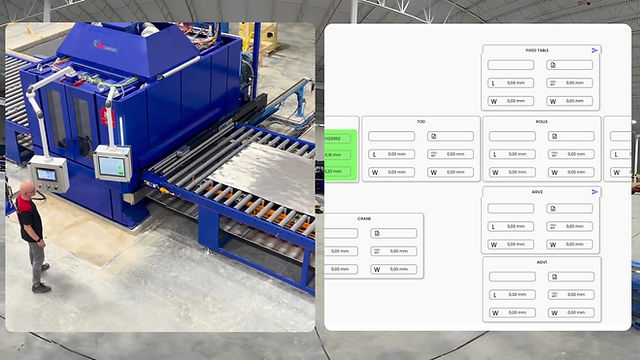
We now have the experience and the right partner to support a Level 2 automation project, where we enable our grinding line to communicate with all other installations within the company and the overarching ERP system.